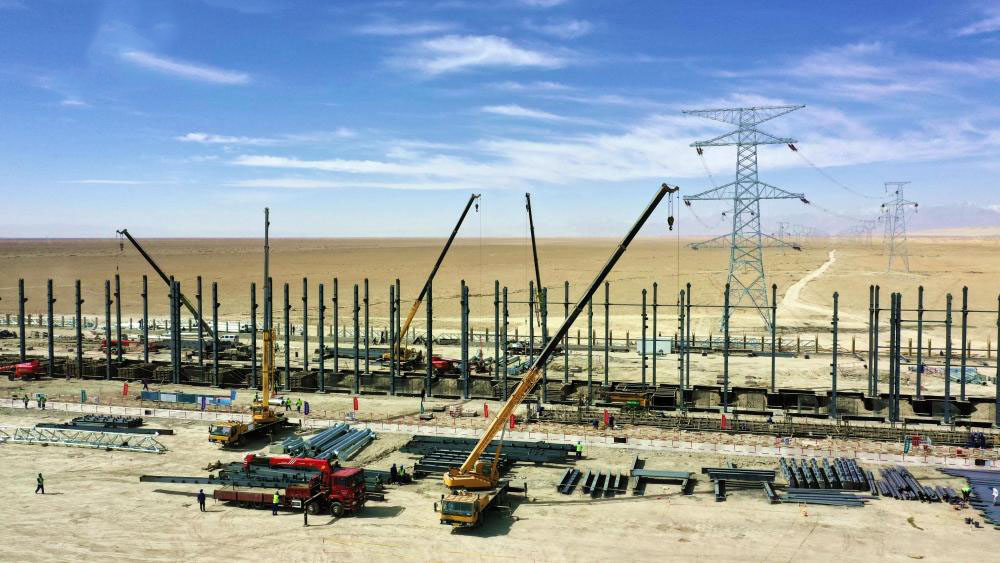
In the development and production process of oil and gas fields, oil and gas well pipes are in the underground environment of high temperature and high pressure, and are eroded by harmful gases such as carbon dioxide and hydrogen sulfide, which leads to serious corrosion of oil and gas well pipes, often resulting in pump leakage, pipe leakage, rod and tube breakage and other hazards, which seriously affect the normal development and production of oil and gas fields. The specific corrosion types and corrosion reasons of the pipes are roughly as follows:
First, pipe corrosion category
1.1. Tubing corrosion
The form of tubing corrosion is mainly electrochemical corrosion, the work of the tubing by the role of high moisture content fluid flow, the formation of a corrosion battery in the inner wall of the tube, due to the battery potential is low, the fluid environment caused by the corrosion of the inner wall of the tubing is light. For gas Wells, the oil jacket ring in the oil pipe is surrounded by corrosive media, and condensation will occur on its surface, forming a corrosion battery. The result of corrosion of the pipe wall is the formation of loose iron sulfide film on the tube wall, and the metal is rapidly destroyed as an anode. For oil and gas Wells with packers, corrosion inhibitors form a good protective film in the oil jacket ring space to prevent external wall corrosion.
1.2. Casing corrosion
Due to the large amount of sulfur in the crude oil, the formation also contains a variety of salts, dissolved oxygen and other harmful gases, these substances are distributed in the form of ions around the oil well casing, and their interaction occurs chemical or electrochemical reactions, resulting in corrosion damage to the oil well casing. In addition, the acid, hydroxide and chloride ions contained in the water medium will cause the chemical corrosion of the oil well casing to accelerate. The salt and alkali components in the formation form a dielectric, which is distributed around the oil well casing to form electrochemical corrosion. Therefore, the chemical and electrochemical corrosion of oil well casing is the main cause of its damage.
1.3. Corrosion of drill pipe
The working conditions of drill pipe in oil well are very bad, especially the corrosion of dissolved oxygen is the most serious. Dissolved oxygen corrosion is oxygen depolarization corrosion, resulting in tan corrosion on the corrosion surface. The most serious is local corrosion on the surface of the drill pipe, with pits or grooves, which intensifies the corrosion of the drill pipe and leads to serious local damage to the drill pipe.
Second, corrosion reasons
2.1. Effects of dissolved salts
Generally, the water produced by the oil field is dissolved in a large number of salts, with a high degree of salinity, the higher the coastal oil field, the higher the salt content, the stronger the electrical conductivity of the water, which accelerates the interaction of the negative and cation on the metal surface, so that the attachment can not be deposited on the metal surface. Chloride, sulfate and bicarbonate are common dissolved salts in oil field water, and chloride and sulfate ions are more corrosive, more likely to cause corrosion damage, so that the oxide film on the surface of the metal is seriously damaged. Therefore, chloride and sulfate ions are also the main reasons for the point corrosion of carbon steel.
2.2. Impact of corrosive gases
The corrosive gases in the oilfield mainly include carbon dioxide (CO2), dissolved oxygen, hydrogen sulfide (H2S), etc. The corrosion of CO2 is mainly manifested in its hydrogen depolarization corrosion. When free carbon dioxide (CO2) reacts chemically with water, carbonate ions are produced, which increases the acidity of water, accelerates the destruction rate of metal protective film, and the resulting corrosion is easily soluble. When there is no antiseptic on the metal surface, the corrosion effect of the metal is further aggravated.
When hydrogen sulfide encounters water, it ionizes, and the ionized hydrogen ions become strong depolarizing agents and transfer to the metal cathode to obtain electrons, which accelerates the anode iron dissolution reaction and leads to the overall corrosion of metal materials. Hydrogen sulfide in oil field water mainly comes from the dissolution of associated gas in water in sulfur-containing oil fields, and H2S corrodes metal materials electrochemical and penetrates into metal materials, making metal materials brittle fracture under the action of stress, that is, hydrogen damage. The concentration of dissolved oxygen has a great influence on the corrosion of metals. The experiment shows that the oxygen content in about 0.1mL/L can cause serious corrosion, with the increase of oxygen concentration of metal material corrosion speed up. The form of corrosion is mainly local corrosion.
2.3. Influence of pH value and temperature
Generally, the corrosion rate of metal in acidic solution will decrease with the increase of pH value; For a solution with a neutral pH value, it does not affect the corrosion rate of the metal because the oxygen depolarization reaction is dominant. When the pH value is alkaline, it leads to the phenomenon of metal passivation, but reduces the corrosion rate. The pH value of the fluid is different, and the percentage of H2S dissolved in water dissociates into H2- and S2- is different, and the effect on corrosion is different. The pH of the water or mud produced from an oil well is generally between 6 and 9. In this range, the pH value generally has no significant effect on the corrosion of metal materials. The reaction rate of cathode and anode in electrochemical corrosion of metal increases with the increase of medium temperature. The higher the temperature, the faster the corrosion rate. The data show that when the medium temperature rises by 10℃, the rate of metal corrosion increases by about 30%. Therefore, for high temperature oil Wells, we should pay attention to the influence of medium temperature, which is a factor that cannot be ignored.
2.4. Influence of biological factors
There are generally three types of bacteria that thrive in oil field production water: Sulfate reducing bacteria (SRB), iron bacteria, saprophytic bacteria, and the biggest harm to the corrosion of oil Wells is SRB, SRB reduces the inorganic sulfate in water to hydrogen sulfide in an oxygen-free environment, thus causing corrosion to the system. There are black FeS in the corrosion products, and the produced water is often black water and smelly, making the equipment suffer serious corrosion. In oil well water samples, some well sulfate-reducing bacteria as high as 105 /ml, the harm degree is quite serious, so it must be controlled.
Third, corrosion protection measures
According to the above corrosion categories and specific corrosion causes, in order to ensure the normal production of oil and gas Wells, effective protective measures must be taken. The protective measures of oil and gas Wells determine the service life of equipment, which is of great benefit to reducing the accident rate, saving production costs, reducing material loss and improving production efficiency. Due to the different production conditions of oil and gas Wells, specific analysis should be done for specific oil and gas Wells, and the application of strong and targeted process methods should be studied to prevent and control corrosion. The protection of oil and gas Wells at home and abroad is mainly considered from the following aspects.
3.1 Suitable pipes
Use corrosion-resistant materials for pipes. Stainless steel, ceramic and other materials of accessories tools, glass fiber reinforced plastic, carbon fiber rod, etc., in severely corroded oil Wells have a very good application effect, but the cost is high, if the use of low cost of ordinary carbon steel tubing, short service life, the need for frequent replacement, the service life of ordinary carbon steel tubing is also difficult to grasp. At present, corrosion-resistant alloy pipe has good anti-corrosion effect and high price, so it is rarely used in domestic medium and low oil and gas Wells.
Use special thread oil well pipe. Special thread (318) oil casing imported from abroad is widely used in deep Wells, ultra-deep Wells, high-pressure gas Wells, heavy oil thermal recovery Wells, directional Wells, heavy corrosion (167ML50) Wells. By some estimates, its market share exceeds 22%. Special threaded oil well tubing with high connection strength and good sealing (104EU) performance is suitable for high-pressure gas Wells, oil Wells and thermal production Wells. Strong bending resistance, suitable for inclined Wells, extended reach Wells, horizontal Wells. Easy to fasten, fast and easy to fasten, suitable for drilling operations in harsh environments such as deserts and oceans.
Choose oil well pipe resistant to CO2 corrosion. It is mainly used in oil Wells with high CO2 content and severe corrosion, and sometimes in corrosive media where CO2, H2S, Cl- coexist, including H2O. There are relatively mature products abroad. In addition to APISpec5CT, which is listed as a 13Cr steel grade (L80-13Cr), each production plant has established its own non-API steel grade. Taking Kawasaki Steel as an example, the four steel grades after its non-API 13Cr are called Super 13Cr.
In order to be more stable in the environment with high CO2 and H2S content, the corrosion resistance of the material is often more stable, and the high content of Ni, Cr stainless steel and Ni-based alloy (TC30) are often used, but due to the high price, the content of Cr element in 2-5% at home and abroad has been developed to resist CO2 corrosion type economic tubing.
3.2. Surface treatment of the pipe
The protection methods of the inner wall of the pipeline include: interface protection, including electrochemical protection by coating anti-corrosion layer; Chemical protection, such as corrosion inhibitors, fungicides, deaerators, etc.; At present, the most common application is to use the anti-corrosion layer in the interface protection, also known as the inner coating (710). Commonly used coatings are: epoxy type, epoxy phenolic type, polyurethane and urushiol type and other main base materials. Primer coating: generally mixed with iron rubinin, chromium yellow and other passivating properties of the pigment filler; Intermediate layer and surface coating: add more scales or glass beads to improve its permeability resistance.
The coating technology of pipeline anti-corrosion layer mainly includes solvent-based spin spraying coating process, fused epoxy coating process, film lining process, cement mortar lining process, continuous coating process, etc. The process is suitable for centralized coating of a single pipe in a special factory production line. Commonly used paint for solvent-based paint, primer and top paint are used together, generally a primer and two to three top paints.
Heat treatment nitriding process for pipe anticorrosion is also a widely used anticorrosion means. Nitriding process is relatively simple, often used for the outer corrosion of oil well pipelines, it has good corrosion resistance and wear resistance, but it is not suitable for corrosive environment.
3.3. Corrosion protection caused by dissolved oxygen
Dissolved oxygen in water is very harmful to metal equipment, etc. In view of the corrosion mechanism, the prevention and treatment of corrosion focuses on the formation of a thin film (Liquilon) adsorption layer on the metal surface to separate the metal from the medium, mainly from the following aspects:
1) No oxygen – take measures to isolate the air and avoid the dissolution of oxygen. For example, the injection tank is protected by natural gas.
2) Deoxygenation – dissolved oxygen not only causes corrosion of equipment, but also causes damage to oil field auxiliaries. Therefore, for the sake of safety, sodium sulfite, formaldehyde, thiourea, hydrazine and other reducing substances are added to the injected water to deoxidize.
3) cathodic protection – the protected metal is used as the cathode, so that enough current passes through the metal invading the water to prevent corrosion.
4) Add sustained-release agent – fatty acid derivatives; Imidazoline and other nitrogen-containing heterocyclic compounds; Water-soluble quaternary ammonium complex; A complex of organophosphorus and sulfur.
To sum up, there are many factors causing corrosion in oil and gas Wells. Only by thoroughly understanding the causes of corrosion of downhole tools and equipment in the production process of oil and gas Wells and taking targeted protective measures can we effectively prevent or reduce the occurrence of oil well corrosion, extend the service life of oil and gas well equipment, and avoid various accidents caused by corrosion. So as to ensure the normal production of oil and gas Wells. (2023-10-18)